

UniSim PRS is a standalone tool for the sizing, rating and validation of pressure relief devices (pressure relief valves and rupture disks) and surrounding pipes (including multiple elements of different diameters). gives the possibility to test blowdown schedules and simulate what-if scenarios throughout the blowdown network, which enables engineering workflow and gives better insight for safety system design.
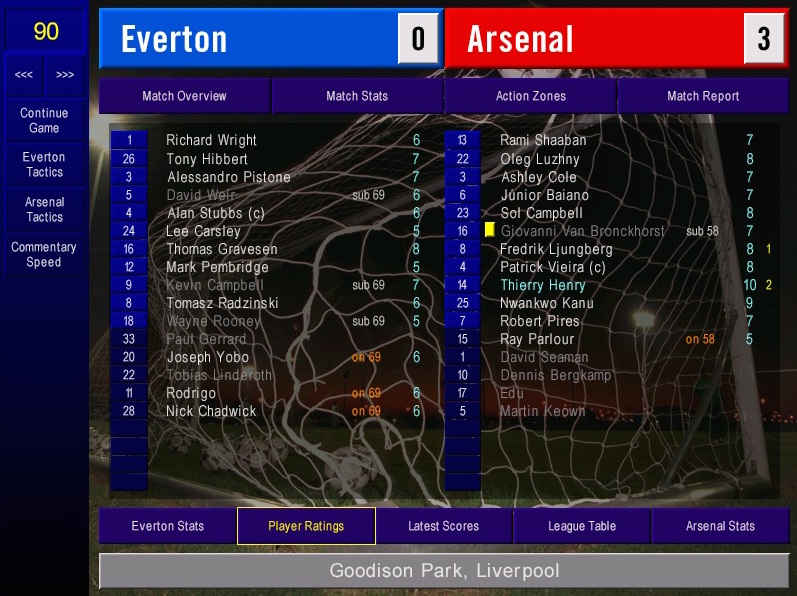
UNISIM DESIGN CRACK SIMULATOR
UniSim Flare is a steady state flare and relief network simulator used to design new flare and vent systems from relief valve to flare tip, or to rate existing systems to ensure that they can handle all possible emergency scenarios. Also, in conjunction with the LP vector generation utility, the refining reactors may be used to generate LP vectors, for use in scheduling and planning tools The refining reactor modules can be calibrated using engineering data or real plant data, leveraging the data reconciliation utility in UniSim Design. The following modules are currently available: UniSim Refining Reactors are unit operations built within the UniSim EO environment and represent kinetic, medium-high fidelity unit operations that reflect refinery conversion units. It includes a number of optimization algorithms (SQP, MINLP and NOVA), allowing UniSim Design to handle more complex optimization problems than the Original Optimizer, and a utility for data reconciliation, which allows models to be matched to operational data. UniSim Optimize is an option in addition to the optimizer which is offered with UniSim Design.
UNISIM DESIGN CRACK OFFLINE
This solver is well suited for solving hundreds of thousands of equations with up to a thousand degrees of freedom, so it can be employed to simulate sizeable processes across all industries, for offline and online applications. An integral part of the UniSim EvOlution platform, the UniSim EO environment leverages Honeywell’s proprietary NOVA solver. UniSim EO is a simulation environment under which equations are solved simultaneously to reach solutions faster, making it suitable for both design and optimization applications. UniSim Case Linker Allows users to link dynamics cases on multiple CPUs. Special features for dynamic modelling include pressure-flow dynamics, a rich set of control functionality to support process control and detailed process monitoring, cause and effect matrices, and an event scheduler. The dynamic model offers rigorous and high-fidelity results with a very fine level of equipment geometry and performance details. A steady-state model can be easily converted into a dynamic model with the use of the dynamics assistant. UniSim Dynamic Option provides dynamic simulation capability and is fully integrated within the UniSim Design environment. It provides an intuitive and interactive process modelling solution that enables engineers to create steady state models through the appropriate selection of thermodynamics properties, feed compositions and conditions unit, control, and logic operations. UniSim Design is the core steady state flowsheeting environment.
